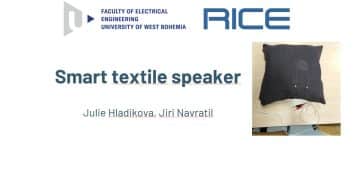
This research paper focuses on the development and evaluation of embroidered textile electroacoustic transducer (speaker).
The paper was presented by Julie Hladikova and Jiri Navratil, Research and Innovation Centre for Electrical Engineering (RICE), University of West Bohemia, Pilsen, Czech Republic at the 4th PCNS 10-14th September 2023, Sønderborg, Denmark as paper No. 2.8. selected by TPC Technical Program Committee as:
PAPER AWARD NOMINATION LIST
ABSTRACT
Smart textiles or e-textiles, represent an evolving trend of electronics that introduce novel perspectives and possibilities for electronic devices. The development of functional smart textile garments relies is closely connected with new materials and technologies, including conductive threads, ribbons, advanced contact technologies, and integration with conventional electronics.
This research paper focuses on the development and evaluation of a textile electroacoustic transducer (speaker). To create the speaker, a hybrid conductive thread is employed for embroidering the coil, while a small magnet is positioned beneath it. When an audio signal is played through the embroidered coil, the interaction of magnetic fields generates forces between the magnet and coil, causing the textile itself to function as a speaker membrane.
The inductor coil’s shape and size are optimized, and the final pattern is embroidered onto tangible textile products, such as a pillow and an elastic sport headband. The frequency characteristics of the tested patterns and textile products are presented. The application of this speaker extends from domains such as well-being, sports, to healthcare.
INTRODUCTION
Smart textiles or e-textiles represent an evolving trend in electronics, where four key technologies together provide powerful opportunities for designing textile garments with special functions. The first technology is the miniaturization of circuits in various shapes and their affordable availability, including integrated circuits, microchips, and memories. The second technology is power management, where new small batteries or energy harvesting systems can be integrated. The third key technology is informational technologies such as IoT (Internet of Things), big data, or AI (Artificial Intelligence) based systems. The fourth key technology is special materials for electronics, including conductive yarns, threads, ribbons and other textiles.
E-textiles have great potential (Fig. 1) in sports, well-being, personal protective equipment, military applications, and are expected to grow in healthcare systems applications (see Fig. 2) hand in hand with telehealth and telemedicine.
While conventional monitoring systems (such as ECG – electrocardiography) are not very comfortable, they are acceptable for short-term or one-time measurements. E-textiles can drastically enhance the wearing comfort for long-term or online diagnostics, monitoring, or treatment of patients.
The healthcare sector, thanks to the measurement of human body parameters, can be connected to military, sports, personal protective equipment, or leisure activities. Therefore, the growth in the healthcare area will likely stimulate growth in other application areas. E-textiles can be divided based on various parameters, including the materials used, the field of application, the manufacturing process, etc. We divide e-textiles based on the level of functional electronics integration into the textiles themselves. Each level brings new possibilities and challenges not only for materials and technologies used but also for future standardization or testing methods. In general, e-textiles can be divided into three groups:
- Conventional electronics integrated into the textile or wearable garment (wearable electronics)
- Using conventional rigid or flexible PCB
- No textile-based electronics components
- Interconnection of electronics device and textile has no more than mechanical functionality
- Low comfort level and integration size restrictions
- Low or no possibility of washing
- Relatively easy to make
- Photovoltaic energy harvesting systems
- Embroidered, knitted, woven or printed parts of electronics such as sensors
- Using textile conductive elements (conductive threads, yarns, ribbons, etc.)
- Using functional printing materials (inks, pastes, etc.)
- Utilizing textile-manufacturing technologies (embroidering, knitting, weaving, etc.)
- Utilizing printing technologies (screen printing, inkjet, dispensing, etc.)
- Taking advantages of CAD software for manufacturing samples or products
- Adapting standard technologies and their parameters for using conductive materials
- Developing new contacting methods for conventional-textile electronics interface
- Updating and adapting testing and evaluation methods
- Electronics is made on the resolution of independent fibers
- Using special plastic fibers to be coated or to be printed by a thread-like sensing structure
- Using plastic optical fibers as a textile-integrated sensor
- Using special high-resolution printing technologies (aerosol jet)
- Using special materials (e.g., graphene, carbon nanotubes, organic materials)
- Battery fibers can power the electronics
references [1], [2], [3], [4]
EXPERIMENT
The experimental part of this work involves the designing, embroidering, and testing of a textile speaker. The concept of a textile electroacoustic transducer is based on an embroidered conductive coil placed on a magnetic element. When an audio signal is played through the embroidered coil, the interaction of magnetic fields creates forces between the magnet and the coil, and the textile itself acts as a membrane for the speaker.
Four designs were created. The coil topologies were designed in Inkscape, an open-source vector graphics editor, using the Ink/Stitch extension. This extension allows editing the embroidery parameters for an embroidery machine. The first topology, labeled A, is a square coil with a side length of 6 cm, embroidered using straight stitches. The second topology, labeled B, is a circular coil with a diameter of 6 cm, also embroidered using straight stitches. The third design, labeled C, is a square coil with a side length of 6 cm, embroidered using zig-zag stitches. The fourth design, labeled D, is a circular coil with a diameter of 6 cm, embroidered using zig-zag stitches (see Fig. 3). Subsequently, three samples were embroidered for each topology.
The first two samples (001, 002) were embroidered on regular cotton fabric. The third sample (003) was embroidered on fabric with a layer of polyurethane (DuPont Intexar). The polyurethane layer was laminated onto the cotton fabric in situ. The samples were embroidered using a semi-automatic embroidery machine, the Brother NV-2600. Hybrid conductive threads with silver-plated conductive microwires were used for the embroidery. After the embroidery process, a small part of each coil was taped over with Dupont Kapton tape to prevent shorting of the entire circuit caused by crossing threads.
Resistance and inductance measurements were conducted on all samples. The resistance of each coil varied from 11.7 Ω to 20.5 Ω. There were no significant differences in resistance values among the samples (i.e., samples A, B, C, and D). However, the inductance showed significant variations between the coils embroidered using straight stitch and those embroidered using zig-zag stitch. The inductance for the straight stitch coils ranged from 3.05 µH to 3.65 µH. In contrast, the measured inductance values for the zig-zag stitch coils ranged from 17.36 µH to 21.62 µH. Refer to Tab. 1 for detailed results.
The next important step involved the measurement of acoustic parameters. The samples were securely attached and gently stretched within the embroidery frame. A magnetic element was positioned on a plywood surface, and the frame with the sample was centered over the magnetic element. The construction of the frame ensured a small gap of a few millimeters between the magnetic element and the embroidery. The sound pressure level was then measured in an anechoic chamber (refer to Fig. 4).
The samples were connected to a voltage source and a signal generator (Bruel & Kjaer LAN XI). The power was maintained at 5 W. Based on previous experiments with infrared thermography, it was determined that the 5 W power was sufficient for generating sound without causing significant heating of the embroidered samples.
The sound pressure level was measured across a spectrum ranging from 16 Hz to 20 kHz, as well as at specific frequencies of 100 Hz, 1 kHz, 10 kHz, and 20 kHz. The highest sound pressure level values were recorded at 1 kHz. The results were notably improved for the polyurethane-coated fabric. The presence of the polyurethane layer renders the fabric locally impermeable, resulting in the speaker exerting a higher acoustic pressure at this frequency.
Sample B, which consists of a circular coil embroidered with straight stitch, was selected as the optimal sample. This pattern was then integrated into actual textile products, namely a sports headband and a pillow. To facilitate testing, a suitable Bluetooth stereo audio receiver with a 2x5W amplifier, in the form of a separate module, was chosen and purchased. The connection between the amplifier cables and the textile coil was established using small, two-piece metal snap button fasteners. One part was soldered onto the cables with a 3D printed housing, while the second part was pressed into the embroidered pads of the coil.
A black polyester elastic sports headband was acquired for the experiment. To simplify the setup, two headbands were layered on top of each other. Polyurethane was locally laminated in the layer closer to the head, where the coil was embroidered. In the layer farther away from the head, a pocket was sewn to hold a small magnet. The amplifier and a power supply (power bank) were attached to the headband. The headband was then placed on an artificial test torso (refer to Fig. 5). The head was equipped with soft outer ear models that incorporated microphones, allowing for the measurement of sound pressure level (refer to Fig. 6).
Next, a pillowcase made of a combination of polyester, cotton, and viscose was purchased. The cover was cut in such a way that a coil could be embroidered onto it. In this instance, no polyurethane laminated layer was used. The pillow was then re-sewn and filled with fleece. It was connected to the same amplifier as the headband (Fig. 7), and the sound pressure level was measured (Fig. 8).
SUMMARY AND CONCLUSIONS
Smart textiles or e-textiles represent an evolving trend in electronics that introduces novel perspectives and possibilities for electronic devices. They can be divided into several categories based on the degree of integration or their functions. Smart textiles find applications in various fields, especially in healthcare, well-being, sports, or protective clothing. The goal of this paper was to create a functional model of a textile electroacoustic transducer. In the current phase of the project, the speaker was embroidered into two textile products: a pillow and an elastic sports headband. The speaker was powered by a power bank and connected to a mobile device via Bluetooth amplifier. The electrical parameters and sound pressure level were measured. The application of the embroidered speaker can range from well-being to healthcare, including generating noise-based sounds for better sleep, waking up, tinnitus treatment, etc.
In the next phase of the experiment, the focus will be brought on the energy source. Powering the pillow with a power bank is possible as it does not significantly hinder its practical use and does not reduce its comfort. The headband, on the other hand, is primarily worn during sports or outdoor activities. Therefore, it is necessary to minimize the power source’s dimensions and weight so that it can be sewn into the headband along with the amplifier, thus not hindering or limiting the user. Resistance tests of individual products are also planned. All textiles need to be durable and able to withstand everyday use. For example, tests of resistance to human sweat or washing cycles will be conducted.
REFERENCES
[1] Fabrice Axisa, P. M. Schmitt, C. Gehin, G. Delhomme, E. McAdams and A. Dittmar, “Flexible technologies and smart clothing for citizen medicine, home healthcare, and disease prevention,” in IEEE Transactions on Information Technology in Biomedicine, vol. 9, no. 3, pp. 325-336, Sept. 2005, doi: 10.1109/TITB.2005.854505.
[2] Seyedin, Shayan, Tian CAREY, Adrees ARBAB, Ladan ESKANDARIAN, Sivasambu BOHM, Jong Min KIM a Felice TORRISI. Fibre electronics: towards scaled-up manufacturing of integrated e-textile systems. Nanoscale [online]. 2021, 13(30), 12818-12847 [cit. 2023-06-19]. ISSN 2040-3364. Available from: doi:10.1039/D1NR02061G
[3] Hirman M, Navratil J, Steiner F, Reboun J, Soukup R, Hamacek A. Study of low-temperature interconnection techniques for instant assembly of electronics on stretchable e-textile ribbons. Textile Research Journal. 2022;92(21-22):4269-4287. doi:10.1177/00405175221084737
[4] Zaman, S.u.; Tao, X.; Cochrane, C.; Koncar, V. Smart E-Textile Systems: A Review for Healthcare Applications. Electronics 2022, 11, 99. https://doi.org/10.3390/electronics11010099
Read the original post at Embroidered Textile Speaker